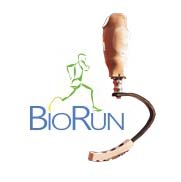
Additive fabrication in parasports by Biorun
September 14, 2023
Founded in 2021 by 5 members of the engineering school ENSMAC – Bordeaux INP (Mechanical and composite material branch), the non-profit BioRun aims at creating a sport prosthesis for amateur athletes.
Biorun’s objective is to develop and fabricate a parasport prostheses maximising biosourced, and/or recycled materials, for tibial amputees steeply reducing pricing compared to commercialy available products.
This is why Biorun chose Nanovia’s biosourced and biodegradable 3D printer filaments, Nanovia PLA Flax, and Nanovia Istroflex.
PLA Flax, is made combining flax fibres from the north of France and a corn starch polymer. Istroflex is a biodegradable polymer (norm EN 13432), reinforced with finely crushed oyster shells from the coasts of southern Brittany, France.
Interview
To get a better overview of the project, we sat down with Maxime Trochon, Biorun’s president.
Who are the members of Biorun, and what is their function?

Given that one of our goals was to make an affordable prosthesis for tibial amputees, we solicited a call for interested people. This led us to work with and integrate into the association Guillaume Ducrocq, a high level parasport athlete with an amputated tibia.
How did Biorun get started?
During our engineering cursus, we were tasked to create an “innovative project”. For this project had a two year limitation but no subject limitation, which leads us to present day.
Since our whole team is into sports and that in 2024 the Olympic as well as the Paralypics are coming to France, we came up with the idea of developing our own tibial running prosthesis.
Furthermore, when looking into how these prostheses are currently made using carbon fibre and epoxy resins, which both are materials that can’t be recycled, the project took a second dimension of maximising biosourced and/or recyclable materials in a societal and environmental context.
Finally, this project has a real possibility of revolutionizing and open the access to sport for tibial amputees.
Currently, how can amputees procure a running “blade” prosthesis?
We performed a survey amongst people in medical fields, amputated athletes and several organisms involved in parasports to better grasp their needs. Which made us realize how hard it is to gain access to running prosthesis.
Once over 18 years old, these prostheses are no longer reimbursed by social security, with prices fluctuating between 10 000 and 20 000 Euros, making it really hard to get one.
The only real way of getting one is by getting sponsored, or if the accident that caused an amputation was done by another person in which case insurance companies might foot the bill.
This makes it that there is no real affordable way for most amateurs to get into the sport. Which is the main goal of our project.
What are the elements of a traditional handisport running blade?
Current tibial running prostheses is composted of three different elements.

- Firstly, a “sock” that covers the remaining member and protects it from friction.
- The fitting, which is the rigid part in which the remaining member is inserted and assures the transmission of movement.
- The blade, absorbs and releases the kinetic energy generated by acting as a spring. The sole acts as the interface of the prosthesis and the ground, protecting the blade, absorbing the impact and stabilizing the runner.
How did Biorun made the blade more comfortable for the athlete?
For the blade, we started by comparing materials that fitted our design specs and studied how we could use them.
We were guided by Terre de Lin (Normandy, France) who shared with us their knowledge of composite materials. For the blade we decided to associate flax fibres (for its French origin and capability to absorb vibrations) and carbon (for its high stiffness and mechanical properties.)
Our wish was to use a thermoplastic, comparatively more eco-friendly to traditional used thermoset (that can’t be melted). Unfortunatly, mechancilly for this specific use case, they are not yet up to specification. Hence why we decided to make our blade with pre-impregnated epoxy resin.
Currently, we have yet to start the certification of the blade since we believe that further research and development would increase its performance and cement it’s chance of passing the norms.
How does using additive manufacturing benefit the fitting ?

One of differentiating factor of our product compared to what exists on the market is the integration eco-conscious design approach by using locally ,biosourced, and/or recyclable materials.
For the fitting’s fabrication, two objectives were set.
This first was to make it easy to fabricate and relatively inexpensive for tibial amputees. We did this by replacing the traditional technique of plaster moulding by using a 3D scanner. This allows for much faster measurements and requires only a little CAO touch-up.
Once we have a 3D file, we can directly 3D print it to get our custom fitting. PLA flax is used since it’s a bio-sourced material (corn starch polymer) and that the flaw reinforcing makes it rigid enough for the application perfectly fitting our economic and ecological goals.
And why Nanovia Istroflex for the sole ?
Istroflex has the cushioning and adherence properties we were looking for for our sole. Unlike other flexibles, and trace materials from wear will biodigrade.
To realise these parts Biorun, partnered with Third, an industrial additive fabrication specialist.

What’s the next step for Biorun ?
The 5 members of Biorun all obtained their engineer certifications in 2023, and we are all going of in different directions.
We are working on handing over Biorun to a team, organisation, or business that is interested in parasports, and would like to push the project forward.
More on Biorun
To learn more about Biorun you can visit them on Linkedin and Instagram.
To learn more about Nanovia’s materials
Image credit : Biorun
Tags: Nanovia Istroflex, Nanovia PLA Flax