Développement d’un filament pour impression 3D sur cahier des charges
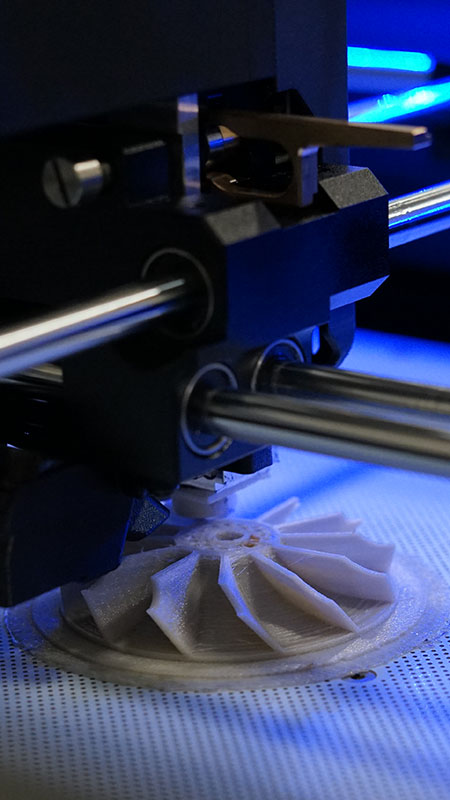
Nanovia est un fabricant et concepteur français de filaments pour impression 3D par dépôt de fil fondu (FFF/FDM). Avec près de 10 ans d’expérience, nous sommes spécialisés dans les filaments renforcés en fibres avec des propriétés adaptées aux industries de pointe.
Notre catalogue propose plus de 30 références de différents polymères. Beaucoup de ces filaments sont nés de collaborations où de créations sur cahier des charges, dont nous allons détailler les étapes ci-dessous.
Sommaire
- Pourquoi développer un filament ?
- Délais de création de filament
- Premier rendez-vous
- Production – compoundage/mélange
- Production – filage
- Tests d’impression 3D de qualification
- Création d’un profil d’impression
- Conditionnement
- Validation
- Comment-nous contacter
- Propriétés additives que nous proposons
Pourquoi développer un filament ?
Souvent nous sommes confrontés à des demandes qui, malgré la forte diversification du marché, n’existent simplement pas et pour lesquelles le besoin est trop limité pour que le marché le satisfait de lui-même.
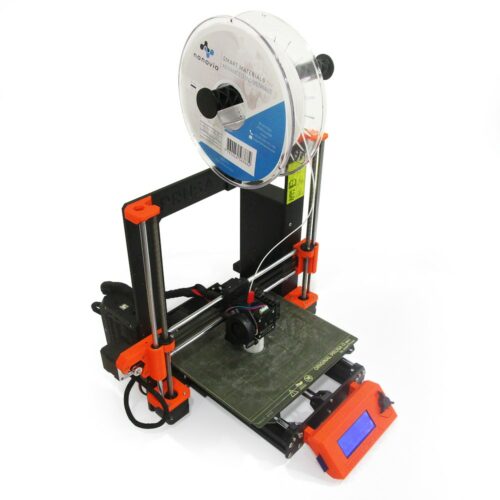
- Recherche d’une résistance, dans des conditions bien particulières, comme des résistances chimiques, à certaines plages de températures, à l’usure, voire des propriétés mécaniques spécifiques.
- Besoin d’une source française/européenne.
- Des besoin de codes couleurs RAL pour des secteurs d’activité
- Pour la création d’une nouvelle marque de filament.
Il est possible de faire des productions à partir de 20 kg selon le polymère. Des « pré-series » plus limités sont également possibles pour certains matériaux plus techniques comme les PEEK/PEKK PEI PSU.
Délais de création de filament
La production du filament se fait sur quelques jours, hors le processus complet prends en général autour de 3 semaines, du premier rendez-vous à la livraison.
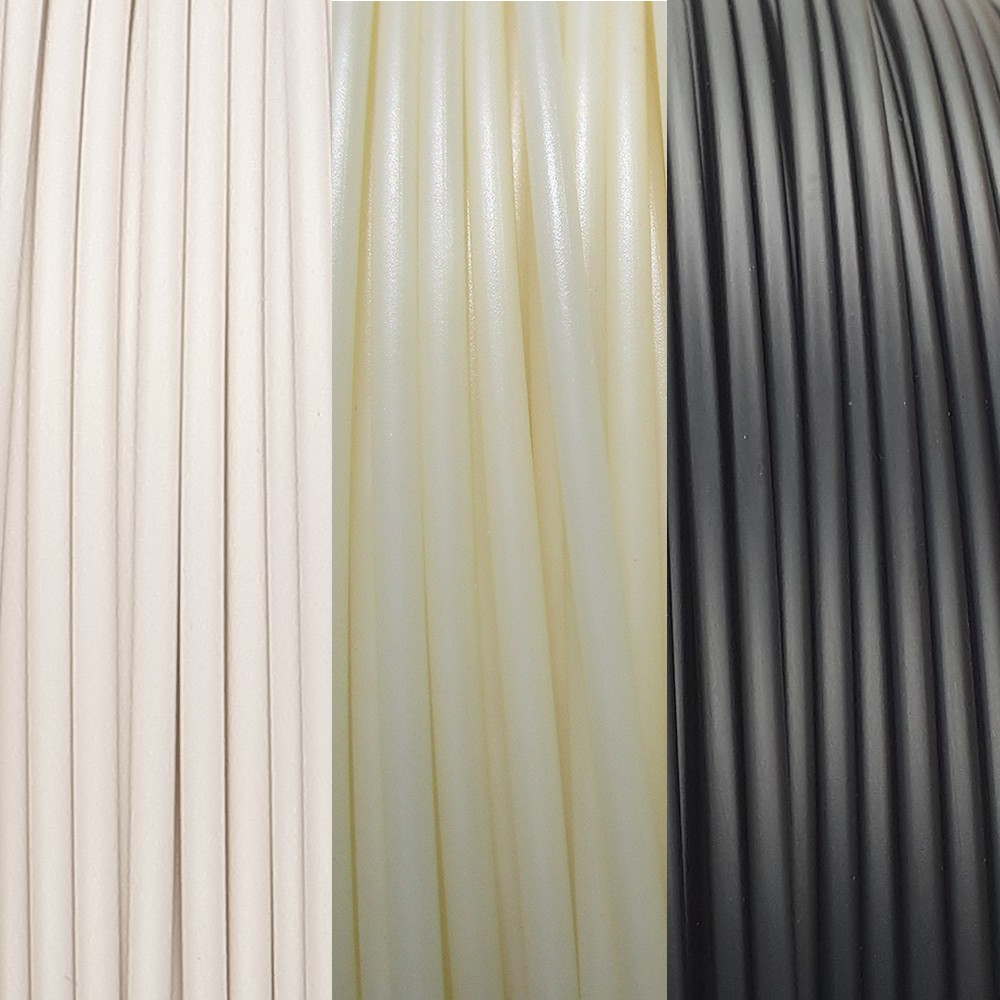
- Premiers rendez-vous – Cahier de charge ( 5 jours )
- Formulation ( 2 jours )
- Approvisionnement ( variable )
- Production – compoundage ( 2 Jours )
- Production – filage ( 2 Jours )
- Test matières ( 1 Jours )
- Conditionnement ( 1 Jours )
- Livraison ( 2 jours )
- Validation client
Premier rendez-vous
Lors du rendez-vous, un de nos ingénieurs matériaux vous aidera à identifier les besoin et les contraintes pour l’usage final du filament.
Ce rendez-vous permet aussi d’identifier les éventuelles limites de production client (limite de température d’imprimante par ex).
Et finalement les volumes nécessaires. Ces étapes permettent de clarifier le cahier de charges et de vous proposer une première formulation.
Cette formulation nous permet d’identifier les fournisseurs de matières premières. C’est en se basant sur leurs délais de livraison ainsi que les différent étapes et les disponibilités de fabrication nécessaires que nous serons capables de vous fournir un devis.
Production – compoundage/mélange
La production de filament pour la majorité des compositions se déroule en deux étapes distinctes. La première étape vise à mélanger tous les composants de manière homogène. C’est l’étape du « Compoundage » (composition en anglais).
Cette étape est réalisée sur une chaine de fabrication dite extrudeuse bi-vis. Cette extrudeuse, comme son nom l’indique, utilise deux vis pour mélanger la matière.

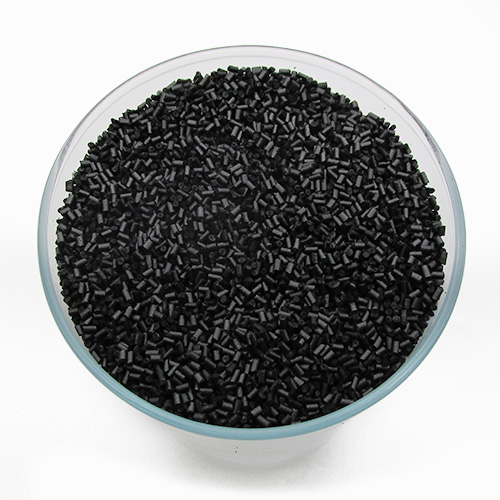
Les éléments de la composition sont alimentés à différents stades de la ligne par des trémies. Selon les propriétés recherchées, l’étape où une matière est insérée modifie les propriétés du produit final. Par exemple, une fibre, plus elle est insérée en amont du procédé, plus court elle sera.
Le jonc qui résulte de ce compoundage est granulé en fin de chaine puis étuvé/séché pendant 24h avant la prochaine étape.
Dans certaines situations, cette étape doit être répétée. C’est le cas pour certains polymères dont les fibres doivent d’abord être composées avec un revêtement d’un autre polymère.
Des versions concentrées (master batch) sont aussi créées pour être mélangées avec du polymère natif dans l’étape suivante. Cette “demi-étape” est utilisée pour certains colorants et additifs.
Production – filage
Le broyat granulaire est de nouveau étuvé, mais cette fois sous vide. Cette étape est nécessaire pour enlever les dernières traces de humidité. Les températures d’extrusions sont assez élevées pour vaporiser l’humidité et créer des porosités dans le filament.
La matière complètement séchée est alimentée par une trémie dans une extrudeur mono-vis. Cette vis est entourée de plusieurs zones de chauffe dont les températures sont réglables individuellement.
Cette vis est également biseautée et un profil de vis spécifique. Cette forme force la matière dans une zone de plus en plus contrainte et augmente la pression progressivement pour extruder un filament parfaitement dense.

Suite a l’extrusion le filament est entrainé dans plusieurs bains de refroidissement sur 15 mètres. Ces bains sont de différents températures et de types de refroidissements. Selon les matières ces bains peuvent contenir des huiles, de l’eau, voir aucune matière pour un refroidissement lent.
Le diamètre du filament est contrôlé au bout de chaine par une mesure laser, ce dernier ajuste la tension du filament pour le régulariser.
Le filament régularisé et refroidit est enroulé sur une bobine « maitre » de 30kg en fin de chaine.
Chaque filament à ses propres paramètres de production uniques.
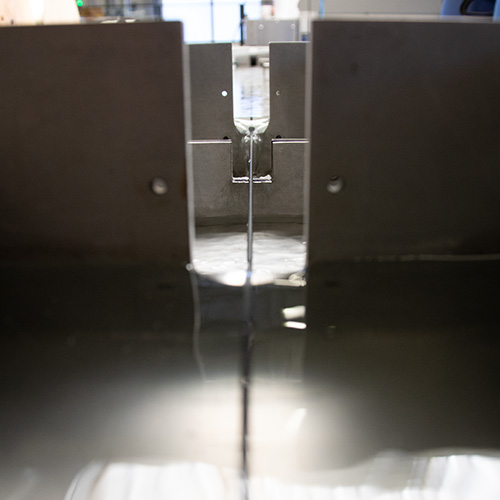
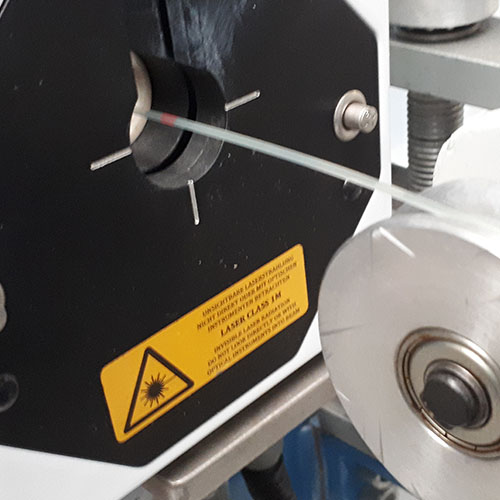
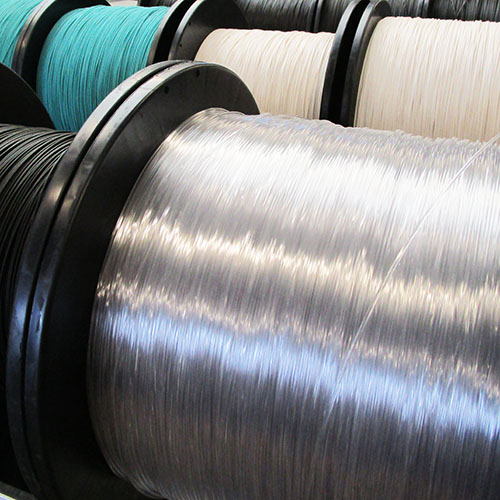
A la fin de la production, le filament normé est de nouveau étuvé pendant 24h pour éliminer toute humidité qui a pu s’introduire via les bains de refroidissements et l’humidité atmosphérique.
Tests d’impression 3D de qualification
Un échantillon du filament étuvé est introduit dans des imprimantes 3D de différents types et configurations afin de tester :
- Que lors de l’introduction il ne se casse pas (trop rigide).
- Pour déterminer avec quel type d’alimentation le filament peut être guidé (si le filament peut être poussé, ou doit être tiré dans le cas de filaments fragiles et souples).
- Déterminer le diamètre de buse nécessaire pour que le filament ne bouche pas lors de l’impression entrainant de la sous-extrusion. Ce qui peut être le cas avec certains filaments fibrés où composites.
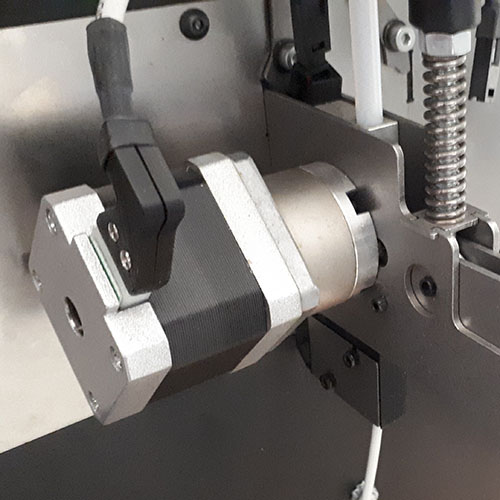
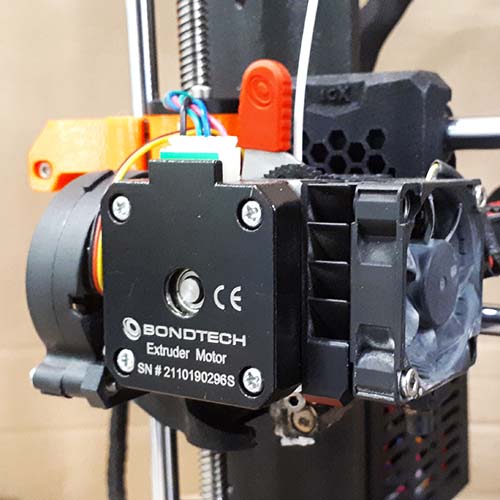

Création d’un profil d’impression 3D
Avec le filament qui passe correctement dans l’imprimante on détermine la température d’impression dans un premier temps avec l’impression de « tours de températures ». Ces tours permettent de vérifier visuellement si la géométrie de la pièce est respectée selon la température.
Puis avec des tests mécaniques de traction sur des éprouvettes normées imprimées dans les plages de températures identifiées.
Cette plage de température reste cependant indicative, comme selon les imprimantes et les conditions ambiants (température et niveau de humidité) le filament a besoin d’une température différente. Nous conseillons toujours de faire un test de tour de température pour cette raison avec votre équipement.
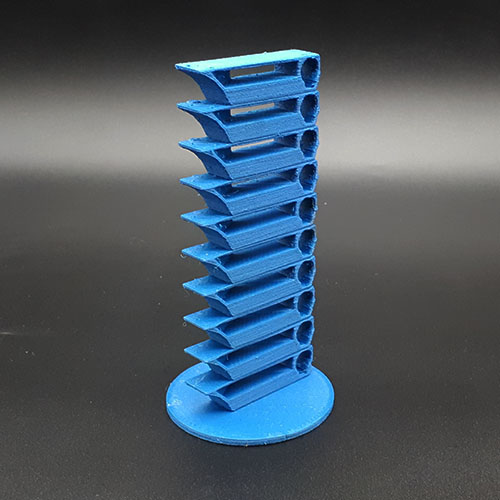

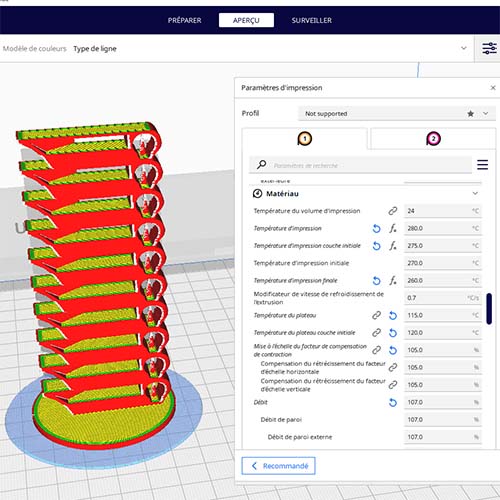
Conditionnement
La dernière étape de production consiste à transférer le filament sur des bobines de taille adaptées au besoin. Nos bobines standards sont en carton recyclés et recyclables, gravées au laser. Nous proposons également d’autres formats et matières de conditionnement.
Pendant cette étape, un contrôle mécanique additionnel de diamètre est appliqué grâce à une filière limitée au diamètre nécessaire.
Certains de nos produits ont des propriétés abrasives, notamment ceux qui sont renforcés en fibres de carbone et de verre ainsi que les composites chargés en céramique. Quand la filière présente des traces d’abrasion elle est remplacé.
Les bobines sont mises sous vide avec un dessiccant pour les conserver anhydres jusqu’à l’impression par le client.
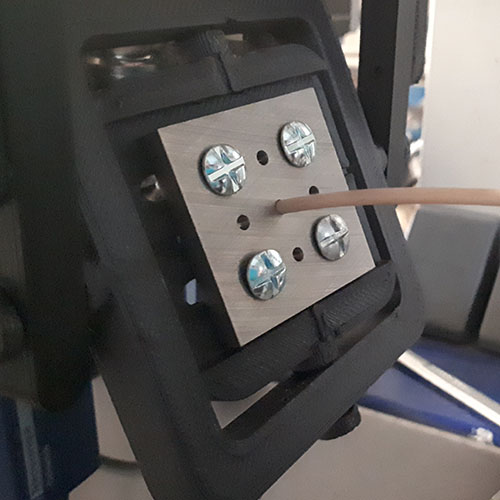
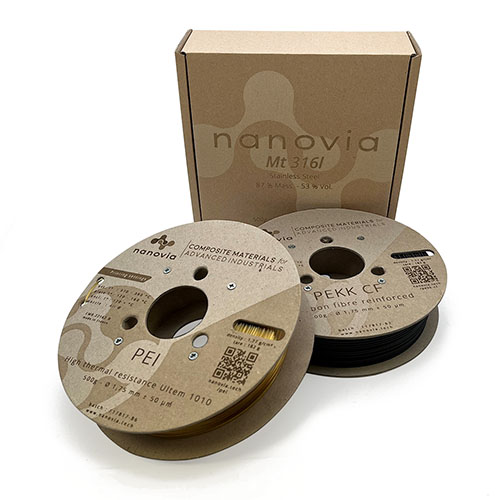
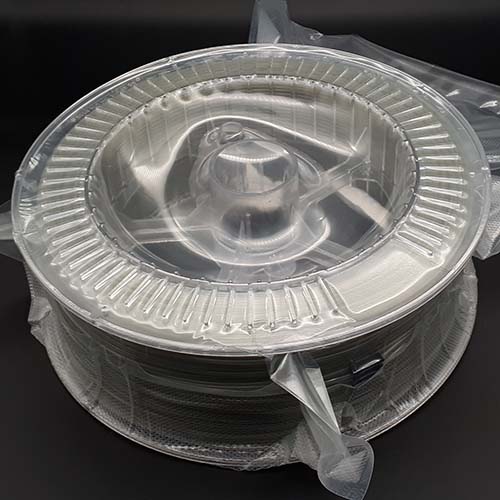
Validation
Il est commun de faire une production test afin que le client valide la formulation. Si le client valide le matériau, il peut être produit a plus grande échelle, souvent avec une augmentation de vitesse de production.
Comment-nous contacter
- Via notre formulaire de contact
- Email : contact@nanovia.tech
- Téléphone : +33 (0) 296 43 36 90
Propriétés additives que nous proposons
Radiation
- Blindage X-Ray
- Blindage ondes radio
- Resistance UV
- Absorption radiation
- etc…
Industrie
- Conducteur
- Isolant
- Virucide / bactericide
- Basse friction
- Détectable metal
- Résistant au feu
- Metal / céramique pour frittage
- etc…
Fibres
- Naturel
- Carbon
- Aramide
- Verre
- Basalt
- Continue
- etc..